Concrete Floor Design and Membranes
Floor Strength and Waterproofing
Good structural design of reinforced concrete floors prevents them from sinking or subsiding and, when combined with the correct use of a waterproof membrane, we can keep the floor dry and avoid rising moisture through the floor.
Here we discuss how subfloors can be incorporated into the structural design of a building.
The Structural design of concrete floors in domestic houses
Subsiding, sinking and even rising floors are common problems when the floors have not been correctly designed and constructed. They need to be stable but this is not always the case is it? Sometimes we are faced with instability beneath our feet. How many sad cases have I seen over the years where beautiful floors in someone's very expensive villa have been seriously damaged by subsidence, cracking or rising moisture.
Of course it all comes down to what is happening underneath. The area in question is the subfloor, the floor beneath the floor - the real floor, the tiles are, after all, only the decoration, the finishing.
Next time you see someone laying some floor tiles just take a look at what is underneath. You will find that the standard method of laying tiles is to smooth out what is underneath (whatever it is, soil, old broken concrete, stones) then put down a 50 mm layer of cement and set the tiles into it. Looks great for a couple of weeks until some Russian arm wrestler comes for tea and steps on a soft patch, tiles crack and move and those mischievous spirits have their wicked way.
While there are some excellent architects and builders around who really know what they are doing there are very many that don't. Even in expensive properties you may find that builders don't pay much attention to the subfloor and architect's drawings rarely provide the necessary detail presumably assuming that the builder will know what he is doing.
Subfloors
We need to understand where the subfloor fits in the overall scheme of things.
The structure of most modern buildings in Indonesia have foundation walls built from large stones. People who know what they are doing will also have reinforced concrete foundation "piers" (short columns that stand on concrete footplates buried in the ground) situated in key locations along these stone walls where concrete columns will be placed to support the walls, roofs and upper floors.
Reinforced concrete "sloof" or ground beams are cast along the top of the foundation walls. These sloof beams hold the foot of the columns together horizontally.
Even buildings built to low cost, local standards that don't have properly designed foundation piers or properly designed columns will still always install sloof beams.
1. Simple floor method
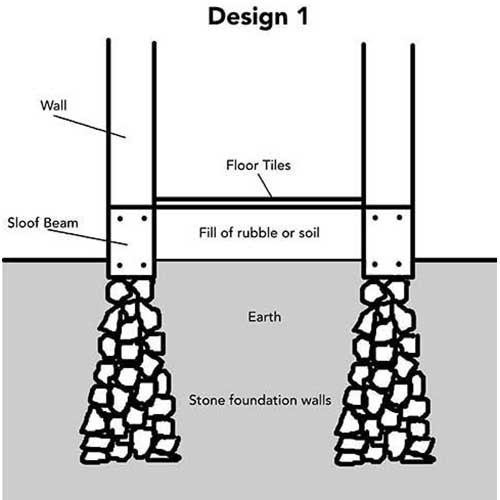
Now when it comes to laying the subfloors the squares between the sloof beams are usually filled to a level surface. Now if the fill is rock or sand this is often not too bad although it should be compacted. If the fill is soil or much worse - clay, this will expand in the wet season and contract in the dry season making the floors rise and sink. If you see someone putting any sort of vegetable matter in the fill you know there will be a problem later when the vegetation starts to rot down - the floor will sink.
In many cases tiles are simply laid on top of this compacted fill, it is hardly surprising that there will be problems.
2. Use of reinforced concrete panels

More enlightened builders will partially fill the voids between the sloof beams with rock and/or sand and will then put a layer of concrete with a steel mesh reinforcement on top of the fill and level with the top of the sloof beams. This method is much better but still has a couple of problems.
There is a vertical joint between the concrete subfloor and the sloof beam which can allow the subfloor to move, moisture may rise up the joint and may also provide a passage for termites. It is quite amazing how small a crack termites can get through. It is common for builders to use a weak mix of concrete for the subfloor - it should be full strength concrete and 100mms thick.
This type of subfloor construction can be improved by securely connecting the sub floor panels to the sloof beams during construction using the reinforcing bar to prevent movement. Modern materials are also available to seal the subfloor concrete to the sloof beams.
These are the most common ways that subfloors are constructed here in Indonesia.
3. Full single slab floor

There is, however, a much better way of constructing a subfloor.
We can cast the whole of the floor as a single reinforced concrete slab that lies across the top of the sloof beams. As long as it is properly designed and constructed it is much stronger and it is far more resistant to dampness or termite penetration from below. You won't get sagging or bulging in the floor and moisture and termite penetration is a much lesser problem.
If the structural engineer and builder know their craft the ground floor and sloof beams can be cast as a single unit but it is important that the formwork is good, that the concrete is well placed and that properly designed beams with strong reinforcement is included.
Waterproof membranes
Well understood in other parts of the world but still little understood in Indonesia is the use of waterproof membranes beneath the subfloor to prevent moisture penetration. In Australia it is common practice to install single large sheets of tough black plastic underneath floor slabs. Unfortunately it is difficult to find suitable plastic sheets in Indonesia.
Builders are starting to use waterproof membranes as standard practice. These are often used in floor design 2 above although this still has the weakness of water penetration between the sloof beams and the floor panels.
The best method is to use a full membrane that provides a single continuous barrier under the floor and the sloof beams as shown in floor design 3.
Waterproof membranes must be well sealed, only a single small hole can render them useless and spell disaster. Care must be taken in their placement to make sure there is no path through which moisture can penetrate, avoid joints and make sure they don't get punctured by sharp items.
Phil Wilson
Copyright © Phil Wilson February 2016
This article, or any part of it, cannot be copied or reproduced without permission from the copyright owner.